Increase Production Efficiency and Product Yield for Robot Arms in the Panel Industry
12/30/2022
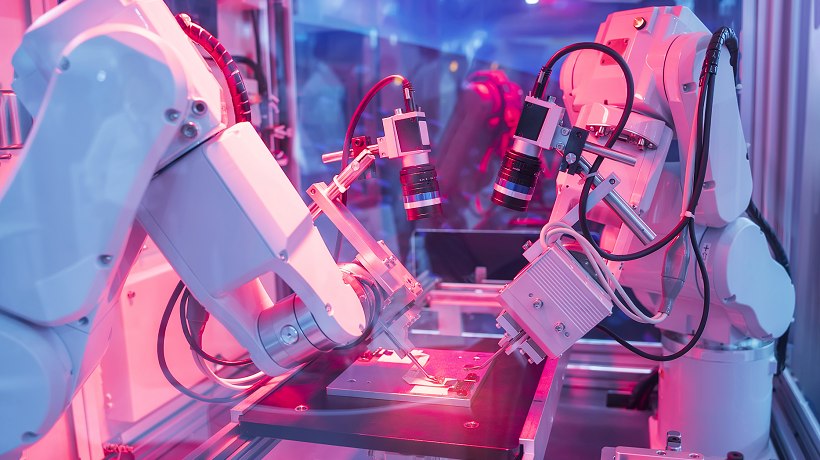
Partner: imCloud CO., LTD.
Region: Taiwan
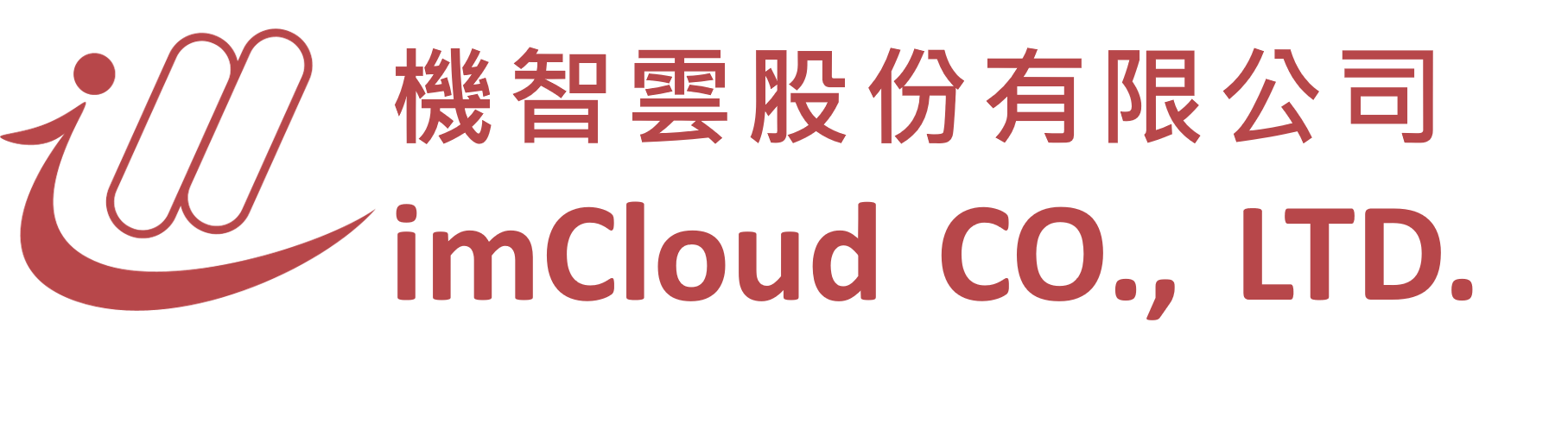
Background
Robot arms have become essential in automated manufacturing and have significantly reduced the need for manpower. They also improve the accuracy of assembly and boost productivity. However, components of these robot arms such as motors, reducers, and bearings suffer wear and tear from prolonged operation, and it leads to decreased positioning accuracy. Maintenance has become a necessity. Disassembling a robot arm for maintenance normally requires professional skills and is time-consuming. Production downtime caused by the unexpected breakdown of robot arms will greatly affect productivity and increase costs.
Requirements
Robot arms are core equipment in automated production lines. A great deal of production time and cost comes from repairs when robot arms unexpectedly go down. Additional time is then needed after repairs for re-alignment and fine-tuning to get production lines back into optimal operation. A Prognostic and Health Management (PHM) embedded predictive maintenance system can be used to ensure stable and reliable operation of robot arms by addressing the following issues:
- Prolonged use of a robot arm without proper maintenance will cause excessive wearing and lead to decreased positioning accuracy. It may continue to operate normally, but unexpected product-quality issues may occur should the arm fail to hold and accurately align the workpieces. This often necessitates stopping the production line for adjustment, which will affect productivity and lead to delayed delivery.
- Excessive wear also causes abnormal arm vibration, which can lead to inaccurate placement of workpieces. This especially impacts precision operations and machining, or the handling of products with a high unit price. Decreased positioning accuracy affects product quality, and the wobbling of an arm can lead to product damage. Numerous products with quality issues will cause significant cost increases.
- Robot arms in automated production lines are high-priced devices. These machines often carry out critical processes that have high-risk or heavy loadings and are often used in hazardous environments. Many factories do not have any engineers who are capable of carrying out robot arm maintenance, so they normally depend on the supplier to provide on-site warranty approved technical support. Factory owners have come to expect advanced monitoring and management of their expensive equipment with early-stage warnings of any anomalies. This allows on-site teams to arrange maintenance and spare parts in advance.
Project Implementation
- IFS-PHM-MIC770W5A : iFactory Edge Machine Predictive Maintenance System
- iFactory PHM I.App: PHM Service Ready Platform
System Diagram
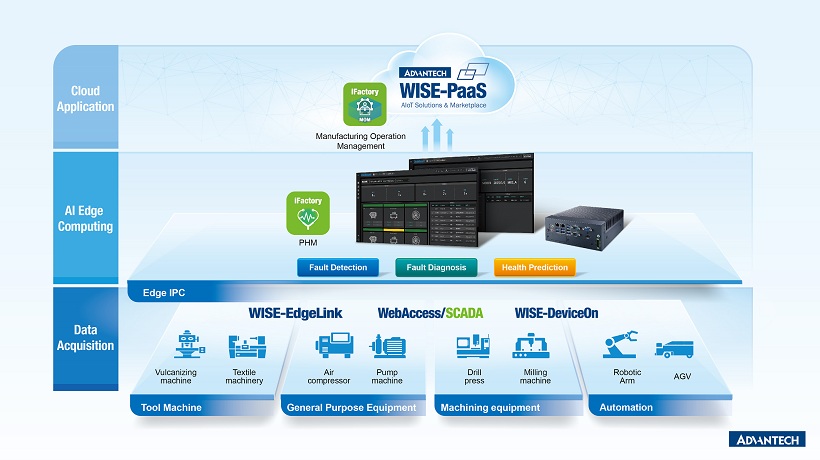
Conclusions
- PHM-based monitoring and fault diagnosis of machines offers an effective method to manage the maintenance of robot arms. Potential device failures can be accurately identified at an early stage and the machine service providers can be notified automatically. The system also makes suggestions in advance about the optimal timing for maintenance work to minimize the impact on scheduled production plans.
- When using an unsupervised learning algorithm, only healthy robot arm data is needed for the implementation of real-time fault detection. This greatly reduces the possibility of unexpected machine downtime which leads to productivity loss.
Customer Testimonial
“After we started using Advantech PHM predictive maintenance solution, our production efficiency and product yield increased significantly,”
Advantech WISE-iFactory: Predictive Analytics
PHM is a machine-centric solution, helping end customers to detect machine anomaly in early stage and provide health state prediction. The information can be used as the decision-making for optimizing maintenance schedule to achieve the goal of smart machine management.